A Guide to Dewatering Screens: Everything You Need to Know
For nearly half a century, dewatering screens have been instrumental in the coal mining industry to effectively separate solids found in slurries. Although sand dewatering equipment may have origins in the coal industry, they have truly found a home across a range of sectors and applications, including pulp paper manufacturing.
Let’s take a closer look at sand dewatering equipment, some of the most compelling benefits, and a few of the key attributes you should know. By the end, you’ll be on your way to becoming a dewatering screen expert.
What Are the Benefits Dewatering Equipment?
Adding dewatering equipment can effectively remove moisture from the final product and capture tiny particles in the wastewater, resulting in drier material. In addition, the removed water can be efficiently recycled back through the manufacturing or processing plant. No matter the industry, the overarching goal of dewatering screens is to deliver the cleanest possible filtrate and driest possible solids.
In addition to creating a drier material, using dewatering equipment offers a range of other benefits. For starters, dewatered material is much easier to handle and can lead to cost savings in transportation.
Material that is dewatered also reduces the drying time of the stockpile, which can free up valuable space at your facility. In some instances, dewatering equipment can reduce or outright eliminate the need for a settling pond. Sand dewatering equipment can lower the amount of material designed for a settling pond.
How Does a Dewatering Screen Work?
The dewatering screen design is relatively simple. The majority of dewatering screen systems utilize two counter-rotating vibrating motors, while some utilize twin eccentric shafts. At the same time, other types of dewatering screens employ multiple mechanical exciters on larger machines that are mounted on a stressed relieved bridge. The drive component is typically set up with an inclined deck that may be set anywhere from three to five degrees. Here’s how dewatering screens work to reduce the water content of slurries:
- The slurry of water and solids is sent down a declined, steeply screened surface to achieve rapid drainage.
- When the slurry passes over the screens, water is drained from the mixture and creates a pool in the valley.
- As the slurry moves through the system, it is taken back up an incline. The screens continuously vibrate throughout the process to help additional water separate from the solution.
- An uphill slope of the screen surface can be combined with a discharge weir to create a deep bed that functions as a filter medium. This allows for even finer solids to be screened out.
- If you would like an even more refined, cleaner product, you can use a rinsing station along the pathway. The sand dewatering equipment can remove the water used for rinsing just as it separates the water from the slurry.
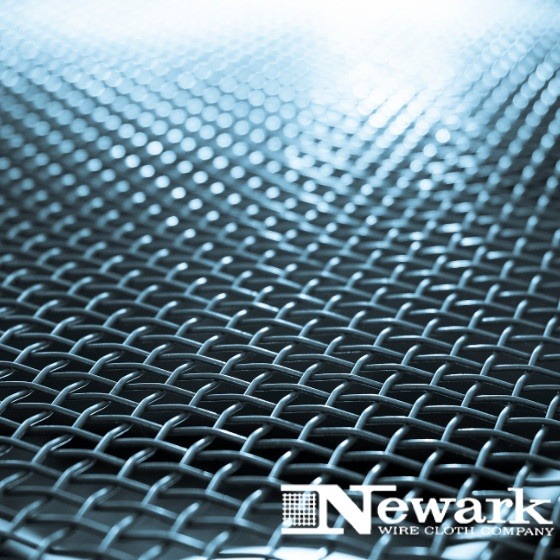
Dewatering Screen Design and Dewatering Screen Sizing
Dewatering screens are capable of processing fine aggregates and achieving dry products from a range of moisture content. However, the ability of the device to achieve the desired results will hinge greatly on the dewatering screen mesh size and design. Here are a few tips and key considerations for choosing the dewatering screen mesh size and dewatering screen design.
The Purpose of the Dewatering Screen
One of the most important attributes to consider in dewatering screen design and size is how it will be used. For finer screening, ultrasonic dewatering screens or rotary dewatering screens may be a more suitable solution. For coarser screening, you may find greater suitability with a straight-line dewatering screen.
The Nature of the Materials
When you’re considering the dewatering screen design and dewatering screen sizing, the nature of the materials is key. While there are several attributes, a few of the most important include:
- — Particle size
- — Viscosity
- — Humidity
- — Bulk specific gravity
- — High temperature
- — Corrosion
- — Static electricity
- — And others
Ideally, the materials being filtered should be compatible with the material used in the dewatering screen design, which can help promote durability and longevity
Working Environment
The dewatering screen design and dewatering screen sizing can both vary based on the working environment. For example, you should take into account whether the working environment is dusty, wet, dry or has needs for fire resistance or explosion proof elements.
Number of Working Hours
The number of hours you expect the dewatering screen to work — whether intermittently or continuously — should be an important consideration.
Material Handling Requirements
You’ll want to select different types of dewatering screens based on your material handling capacity requirements.
Takeaways
- — Dewatering screens have been used in the coal mining industry for over 40 years.
- — The goal of dewatering screens is to deliver the cleanest possible filtrate and driest possible solids.
- — Dewatering screens use a relatively simple mechanism to filter materials.
- — There are several factors to consider when choosing the most suitable dewatering screen mesh size and design.
Contact Newark Wire to Find the Best Dewatering Screen
Choosing the best dewatering screen can be confusing due to the number of moving parts you should consider. However, the experts and engineers at Newark Wire offer decades of experience and will help guide you to the best solution. We’ll listen to your needs, parameters, and then guide you to the most suitable dewatering screen mesh size and dewatering screen design.
Contact Newark Wire today to find the most suitable dewatering screen for your application.